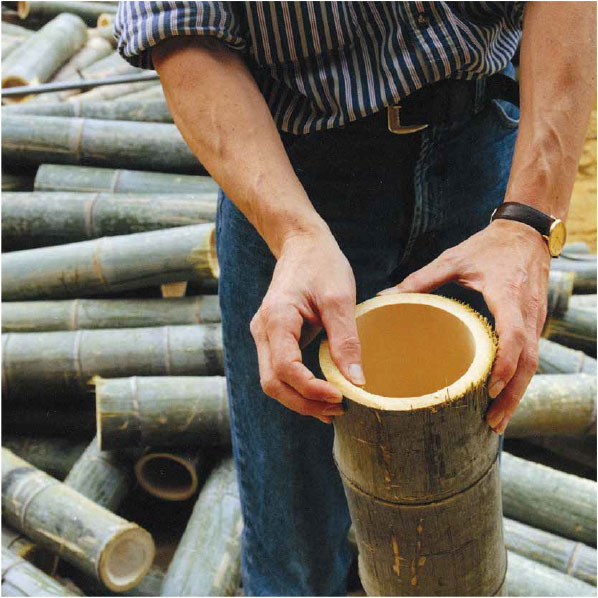

From Bamboo Plant to Product
Transforming a hollow bamboo stem into a high quality MOSO® product –
How is it Done? With almost 20 years of experience in the bamboo industry, MOSO has learnt to manage the production process to perfection.
Stem to Strip After 4-5 years the bamboo stems are ready for harvest. This is very fast compared to (tropical) hardwoods and one of the main reasons why bamboo is ecological. After harvesting the stems are split lengthwise to strips and the outer skin (bark) is removed. Naturally, the strips have a light yellow colour (natural), but can they be steamed to acquire a light brown colour (caramel). Alternatively, they can be thermally treated to acquire a dark brown colour (chocolate).
Assembly of strips After drying the strips are assembled into the end product in various ways, resulting in the following versions (looks).
Plain Pressed (PP)
In the Plain Pressed version the bamboo strips are positioned horizontally and glued together. This creates an elegant line pattern with the characteristic bamboo nodes clearly visible.
Side Pressed (SP)
In the Side Pressed version the bamboo strips are positioned vertically and glued together. This creates a narrow line pattern with the bamboo nodes visible in a subtle way.
High Density® (HD)
Here the bamboo strips are crushed and then glued under extremely high pressure. This compression increases the density – from around 700kg/m3 to more than 1000kg/m3! – which makes the final product much harder. The look of High Density® bamboo is unique: it largely resembles wood with the typical “flames” with the bamboo nodes only slightly visible.
Flexible (F)
In this version the strips are connected using a flexible latex or fabric backing. In addition to using 17 mm wide solid strips also 50mm wide veneered strips can be used.